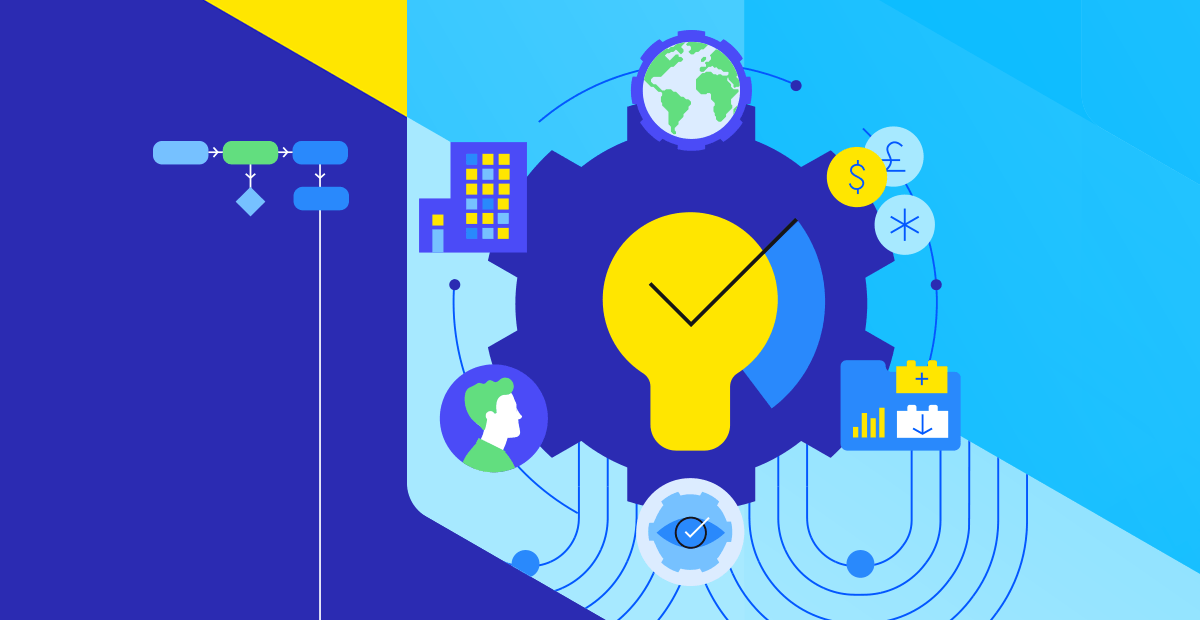
Besondere Herausforderungen bei der Auftragsfertigung
Ob Luft-, Raumfahrt, Schienenverkehr, Schiffbau oder Pharmabranche: Innerhalb von Industrien, in denen die Auftragsfertigung überwiegt, spielen die Kosten für Konstruktion und Produktion selten eine vorrangige Rolle. Alle Teams konzentrieren sich in erster Linie auf die Qualität des Endprodukts sowie die Funktionalität aller Komponenten und deren ordnungsgemäße Integration in das Endprodukt selbst, unter Einhaltung der erforderlichen Spezifikationen. Geht es um Aufträge in Höhe von Dutzenden oder gar Hunderten von Millionen Euro, mag es durchaus trivial erscheinen, dass man sich auf die Optimierung der Grundkosten des einen oder anderen Einzelteils konzentriert.
Doch der immer stärker wachsende internationale Wettbewerb verändert den Status quo wesentlich. Unternehmen müssen heute so schnell und effektiv wie möglich auf die Anforderungen öffentlicher Auftraggeber und globaler Kunden reagieren. Die Optimierung der Produktkosten und der Lieferzeiten darf daher nicht erst im Nachhinein betrachtet werden.
Ein Progress-Kunde, der Auftragsfertigung betreibt, wollte eine stärkere Standardisierung erreichen, um seine Kosten zu optimieren. Als Konsequenz implementierte das Team einen Design-to-Cost-Ansatz, der in der Automobilindustrie bereits weit verbreitet ist.
Alle Produkte des Unternehmens unterliegen ihren eigenen Design- und Industrialisierungsprozessen, bei denen individuelle Eigenschaften zur vertragskonformen Erfüllung der Anforderungen berücksichtigt werden müssen. Der Kunde sah sich folglich mit verschiedenen unternehmensspezifischen Herausforderungen konfrontiert. Jedes Projekt hatte bisher etwa seine eigene Nomenklatur. So war es nicht ungewöhnlich, dass ein Dutzend verschiedene Bezeichnungen für ein und dasselbe Teil existierten - in diesem Fall für mehrere Millionen Teile. Im Laufe der Zeit entstand eine komplexe Reihe von Informationssystemen und isolierten Datenstrukturen, die sich nur schwer nutzen ließen.
Kostenoptimierung vom kleinsten Einzelteil hin bis zum Fertigprodukt
Weil die Produkte wenig bis gar nicht standardisiert waren, unterschieden sich sämtliche Vorgänge. Die an einem Projekt beteiligten Teams, manchmal auf verschiedene Standorte verteilt, arbeiteten jeweils an einem bestimmten Segment des Gesamtprojekts. Sie verwendeten ihre eigenen Tools und ihre eigene Nomenklatur. Eine große Variabilität galt gleichermaßen für Design-, Konstruktions- und Einkaufsprozesse.
Ingenieure, Hersteller und Einkäufer hatten alle ihre eigenen Referenz- und Managementsysteme. Eine globale Kostenkalkulation setzte folglich voraus, dass alle Elemente identifiziert und die einzelnen Stücklisten abgeglichen wurden. Die Einzelteile mussten über den gesamten Fertigungszyklus hinweg miteinander verknüpft, identische Teile mit unterschiedlichen Namen oder Referenzen abgeglichen werden, damit sich die Preise verschiedener Lieferanten vergleichen ließen. Anschließend konsolidierten die Teams alles zu einem vollständigen Produkt. Mit mehreren Informationssystemen und Datenstrukturen schien dies wie eine unlösbare Aufgabe.
Der Einsatz von Progress MarkLogic versetzte das Unternehmen in die Lage, alle Daten zu Teilen und Kosteninformationen aus fünfzehn Jahren Produktion in eine einzige gemeinsame Datendrehscheibe zu integrieren. Diese ermöglichte unzählige Abstimmungen und Vergleiche. Jede Gruppe konnte dabei ihre jeweiligen Identifizierungsprozesse beibehalten. Die Stücklisten der verschiedenen Nutzer (Konstrukteure, Fertigungsunternehmen, Einkäufer) wurden abgeglichen. Daraufhin konnten für denselben Zweck verwendete Teile in verschiedenen Werken gegenübergestellt und bereits abgeschlossene Projekte gebenchmarkt werden. Außerdem wurde es möglich, identische Teile oder Teile mit ähnlichen Eigenschaften für dieselbe Funktion zu identifizieren – zu optimalen Konditionen.
MarkLogic verschafft Einkäufern Einblicke, die ihnen helfen, effektiv mit Lieferanten zu verhandeln und Kosten zu senken, bei gleichzeitiger Minimierung der Fertigungszeiten und Optimierung der Produktionsabläufe.
Intelligentes, optimiertes Design
Bei der Anpassung der Spezifikationen an die Realität der Produktionslinien kam es aufgrund der Vielzahl von Einzelteilen und Teams, die häufig in Silos arbeiteten, innerhalb aller Herstellungsphasen regelmäßig zu einem kostspieligen Hin und Her mit Ingenieuren. Die neue Zielsetzung hieß nun: Ingenieure müssten die Kosten der von ihnen durchgeführten Projekte minimieren. Deshalb war es für die Ingenieure notwendig zu verstehen, wie sich ihre Konstruktionsentscheidungen auf die Gesamtkosten des Produkts auswirkten.
Heute hat das Team einen globalen Überblick über die Kosten, die dem V-Modell vorgelagert sind. Die mithilfe von MarkLogic aufgebaute Datendrehscheibe ermöglicht die Bewertung der Teilekosten in jeder Phase des Fertigungszyklus. Außerdem erfolgen die wöchentliche Aktualisierung von Stücklisten und die Teilebewertung jetzt automatisch.
Der Abgleich der Stücklisten führt zu einer Konsolidierung der Kosten und Ingenieure werden vor Budgetüberschreitungen gewarnt. Das wiederum optimiert die Abläufe in der gesamten Fertigungskette.
Faktenbasiertes Engagement und verstärkter Fokus auf Design to Cost
Zunächst wirkte eine Zusammenführung der Teile- und Kostendaten in einem einzigen System wie ein aussichtsloses Unterfangen. Insbesondere, weil ein internationaler Hersteller dieser Größe über Jahre hinweg Datensilos aufgebaut hatte und über Dutzende von Datenstrukturen, die Fusionen und Akquisitionen mit sich brachten, verfügte.
Nach der Validierung der MarkLogic-Lösung verwandelte sich die anfängliche Skepsis des Teams in Zuversicht. Das Unternehmen glaubte endlich daran, seine Vision verwirklichen zu können. Schon in den ersten Phasen des Projekts wurden verschiedene Nutzer einbezogen, damit sie die Datenquellen besser verstehen und bei der Festlegung der Prioritäten für die ersten Versionen der Datendrehscheibe helfen konnten. Die ersten Abgleiche lieferten wertvolle Daten, sodass die Nutzer die Lösung überzeugt mitgestalteten und bereit waren, notwendige Anpassungen schnell vorzunehmen.
Durch den Abgleich der zuvor getrennt aufbewahrten Daten identifizierten die Nutzer neue Anwendungsfälle, was die Freigabe von Budgets erleichterte. Die Lösung ermöglichte es dem Unternehmen, sowohl organisatorische als auch technische Silos aufzubrechen. Das Resultat sind bereichsübergreifende Zusammenarbeit und intensiver Austausch zwischen den Teams – von den vorgelagerten Phasen des Produktdesigns bis hin zu einer gemeinsamen Kostenkultur und der Umstellung auf einen Design-to-Cost-Ansatz.
„Ihr habt alle zum Träumen gebracht und ihr habt es geschafft!“
So würdigt der VP of Information Systems and Technology die Design-to-Cost-Teams, die dieses Projekt im Rahmen des Build-to-Order-Prozesses geleitet haben. In nur wenigen Monaten verdreifachte sich die Nutzerzahl der MarkLogic-Lösung auf Tausende von regelmäßigen Nutzern, darunter sind Ingenieure, andere Hersteller und Einkäufer.
Dank der Produktkostenplattform oder „Should Costing Platform“, wie sie in der Branche auch genannt wird, ist der Vergleich verschiedener in der Vergangenheit durchgeführter Konfigurationen möglich. So kann sich das Unternehmen prompt und präzise auf Ausschreibungen bewerben.
Monique Bruins
Leidenschaftlicher internationaler Marketingexperte für B2B im IKT-Bereich. Ich unterstütze Kunden und Partner dabei, Innovationen voranzutreiben, um ihr Geschäft mithilfe von IT weiterzuentwickeln.